Corundum fire bricks refer to refractory bricks with Al2O3 content greater than 90%, normal temperature compressive strength up to 340MPa, load softening temperature greater than 1700 ℃, and hardness up to Mohs 9. Corundum fire brick has good chemical stability and strong resistance to acid or alkaline slag, metal and glass liquid. The thermal shock stability of corundum fire brick is related to its structure. The dense products have good corrosion resistance, but the thermal shock stability is poor.
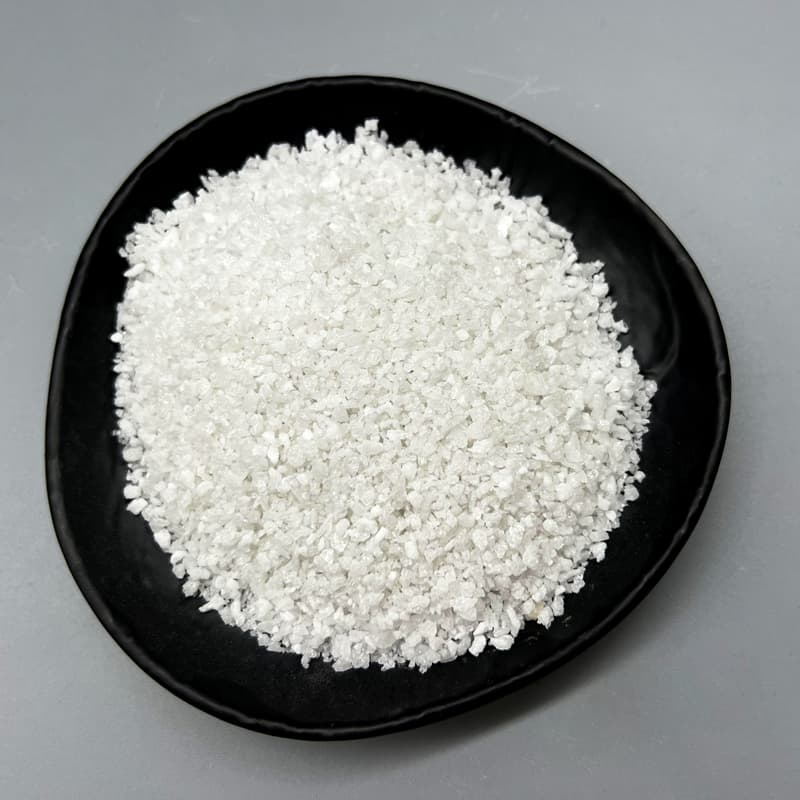
According to the production process, corundum raw materials can be divided into sintered corundum and fused corundum.
1.Sintered corundum
Sintered corundum refers to the refractory clinker made from calcined alumina (or industrial alumina) as raw material, ground into pellets or green bodies, and sintered at 1750~1950 ℃. The apparent porosity of sintered corundum containing more than 99% Al2O3 is less than 4.0%, and the bulk density reaches 3.55g · cm ³. It has good volume stability and chemical stability at high temperature, and is not subject to the erosion of reducing atmosphere, molten glass and molten metal. It has good mechanical strength and wear resistance at room temperature and high temperature.
A. Alumina sintered corundum
Industrial alumina is commonly used as raw material in the refractory industry and sintered at high temperature. The fineness of alumina has an important influence on the density of sintered alumina. Because the calcination temperature of industrial alumina is about 1750~1950 ℃, it is mostly used for calcination in rotary kiln or shaft kiln. When Al2O3 content is low, alumina sintered corundum can also be calcined in tunnel kiln.
B. Tabular corundum
The tabular corundum refers to its crystal in tabular and short columnar structure, which is white and can be produced by sintering and electrofusion. At present, most of the market is sintered tabular corundum. Tabular alumina, also known as tabular corundum, is a recrystallization that is rapidly sintered and thoroughly sintered at a high temperature above 1900 ℃ α- Al2O3 has excellent heating volume stability and thermal shock resistance.
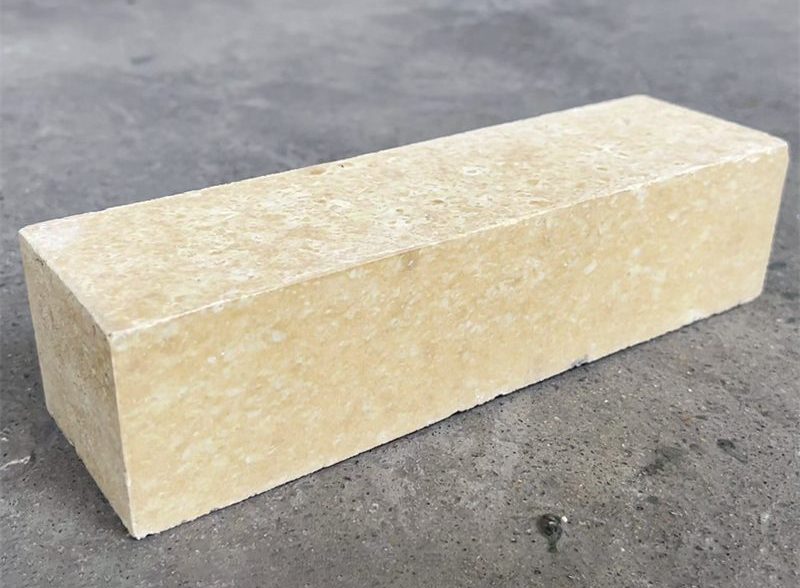
2.Fused corundum
The fused corundum is made of calcined alumina or bauxite. According to the different raw materials and smelting process, the common varieties are: fused white corundum, fused brown corundum, dense fused corundum (low gas pore corundum), high alumina corundum and zircon corundum.
A. White corundum
White corundum, also known as “fused alumina”, is made from industrial alumina by melting at high temperature in the electric arc furnace. Its Al2O3 content is not less than 99%, white, block material, apparent porosity is 6%~10%, the main crystal phase is a-Al2O3, and the crystal is elongated and rhombic.
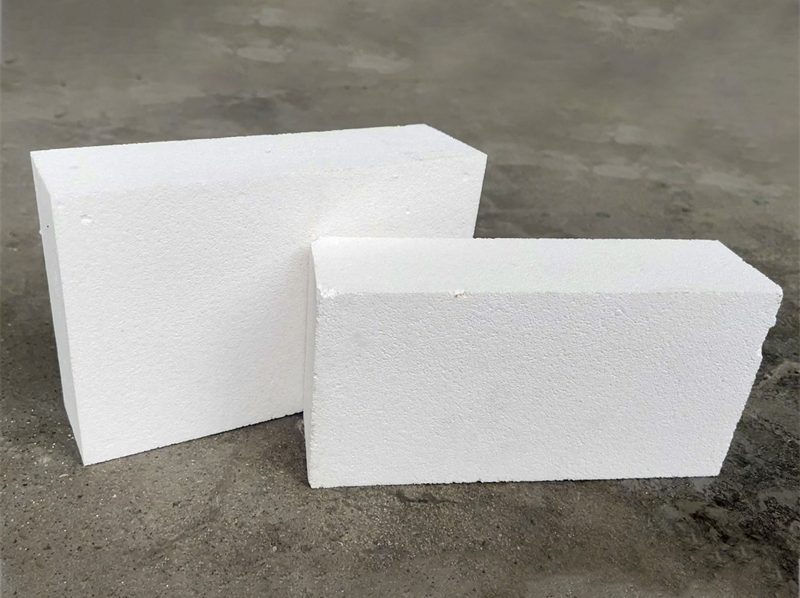
B. Dense corundum
Dense fused corundum is made from industrial alumina as raw material, adding additives and melting in electric furnace. The appearance of dense fused corundum is gray, gray-black or gray-white. Al2O3 is more than 98%, the apparent porosity is lower than that of fused white corundum, generally less than 4%, and the bulk density is more than 3.8g · cm3.
C. High alumina corundum
High-alumina corundum is made by melting the light burned extra-grade or first-grade bauxite loose material with reducing agent, settling agent and other electric arc furnace, and its appearance and physical and chemical indexes are close to that of dense corundum. Its physical and chemical indexes are close to that of dense fused corundum, and its color is also close. Generally, the content of Al2O3 is more than 97%, the apparent porosity is less than 4%, and the thermal expansion coefficient is higher than that of dense fused corundum.
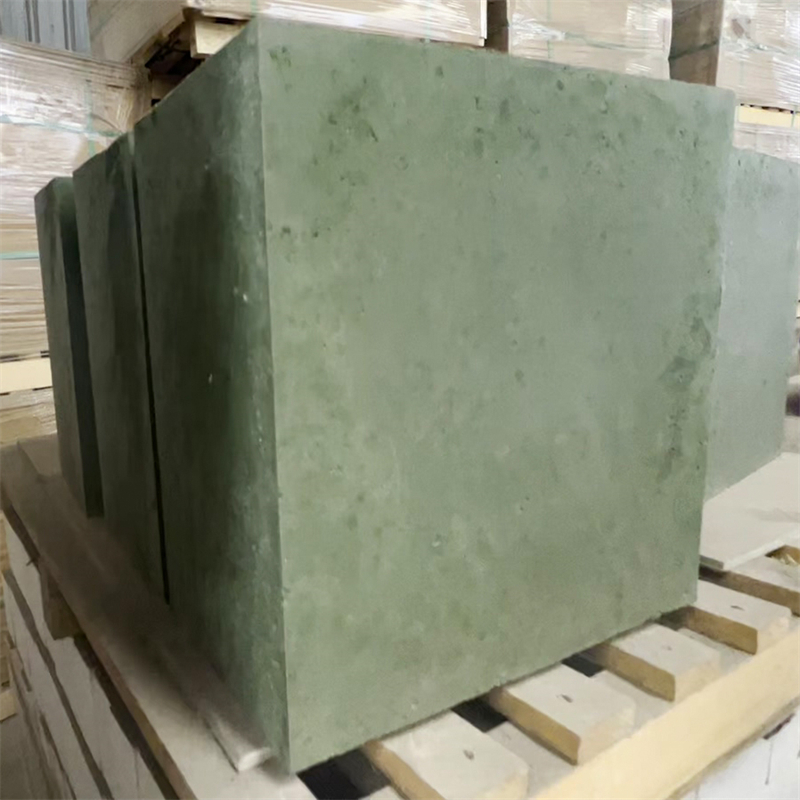
D. Brown corundum
Brown corundum is made by melting natural high-alumina light-fired materials and carbon materials with a small amount of iron filings in the electric arc furnace.