Industrial boiler, as a high temperature industrial equipment in petrochemical industry, is widely used in various fields. With the development of non coal fired boiler and biomass boiler, the requirements for refractory bricks, castables and other materials will be further improved.
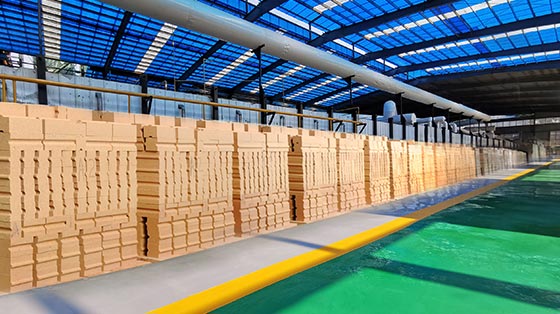
Construction method of refractory masonry for industrial boiler
1.The following conditions shall be met before masonry
1) The metal components of the furnace body (such as steam drum, pipe, beam, door frame, etc.) are installed up to standard and have been grouted twice;
2) The boiler passed the water pressure test;
3) The installation quality, flatness and mutual distance of all parts and water pipes connected with refractory masonry or built into the wall meet the requirements of design and masonry;
4) The installation quality of the pipe or hanger hanging the vault meets the masonry requirements of the hanging brick.
2.Masonry of furnace body
1) In order to improve the integrity of the masonry, for the furnace wall composed of clay brick and red brick, the clay brick should be inserted into the red brick masonry by extending half the brick length every 1.3-1.5m in the height direction and every two bricks in the horizontal direction.
2)When the furnace wall is built above the grate, a short metal pipe (20 mm in diameter) or a hole (60 mm x 60 mm) shall be embedded in the front and back walls and the outer walls of the left and right walls at an interval of 2-2.5 m horizontally to facilitate the water vapor in the masonry to be discharged during the oven drying.
3)Attention should be paid to the cleaning of masonry in the process of masonry, and the residual mud on the surface of brick wall should be removed in time. There shall be no mud, broken bricks and other debris between the refractory brick wall and the water wall tube, so as not to hinder the free expansion of the tube when heated.
4)Flame wall is a special part of boiler masonry, which is usually made of special-shaped bricks. Before masonry, check whether the relevant pipes meet the masonry requirements and whether the pipe spacing meets the design requirements. During masonry, the height of bricks in each layer shall be consistent. Special shaped bricks with fixed bolt holes shall be dry laid layer by layer, and the position of bolt holes shall be marked on the pipe before welding the fixed bolts.
5)The draw hook of furnace wall draw brick shall be placed according to the design position, and shall be kept horizontal, and its quantity shall not be reduced arbitrarily. The special-shaped brick at the draw hook of the water wall should not jam the ear plate of the water wall and affect the expansion of the water wall.
6)When the metal components (such as pipes, steam drums, beams, door frames, etc.) are built in the furnace wall, embedded in the refractory castables or across the furnace wall, the metal components shall be wrapped with asbestos ropes with a diameter of 10-15mm.
7)When hanging the arch roof, if the hanging bricks need to be processed, the strength of the main stressed parts shall not be weakened. At the same time, the fitting clearance of the repaired lifting hole shall not be greater than 5mm.
8)After the furnace body is built, the mud adhered to the outer surface of the red brick shall be cleaned, and the brick joints shall be tightly hooked with cement mortar to prevent air leakage during production.
9)The method of prefabrication on the ground and then hoisting should be adopted for the construction of pipe laying furnace wall: firstly, the pipes of the furnace wall should be placed on the temporary platform, and then the refractory castables and heat insulation castables should be poured layer by layer; After curing and hardening, the whole hoisting shall be carried out.
3.Expansion joint
1)During boiler production, refractory masonry and its connected metal components are heated and expanded to move. Therefore, the setting of expansion joint in masonry is a complex problem, which should be paid special attention to.
2)The size of expansion joint shall be set according to the design template, and the allowable error shall not exceed – 1 ~ + 2mm. The expansion joint shall be even and straight, the inside of the joint shall be kept clean, and asbestos rope or refractory fiber with diameter slightly larger than the width of the joint shall be filled. An asbestos rope close to the fire surface shall be soaked with refractory mud. The asbestos rope shall be flush with the refractory brick wall, and shall not be convex or concave.
3)Fire resistant fiber or asbestos board shall be laid at the contact between column and beam in furnace wall and refractory masonry.
4)In order to ensure that the furnace wall and pipe can expand freely after heating, the gap between them should be strictly controlled during masonry to ensure that the size error does not exceed the specified value.
5)When the expansion joint is set between the flame break wall and the furnace wall, the dimension error shall not exceed 0 ~ + 5mm, and the joint shall be tightly filled with asbestos rope.
6)When hanging arch roof for masonry, expansion joint shall be reserved at the contact between arch roof edge and furnace wall according to design.
7)In order to control the position and size of the straight expansion joint in the refractory castable lining, the wood template should be placed in advance and fixed in the formwork.
In addition to the general requirements, the construction of refractory castables for boilers should also comply with the requirement that the surface of steel bars in the castables should be coated with asphalt layer; The surface of pipes or other embedded parts passing through castables must be derusted and wrapped with asbestos rope, oil paper, etc. according to the design.